Exploring the Die Casting Mould Factory: Innovations and Applications
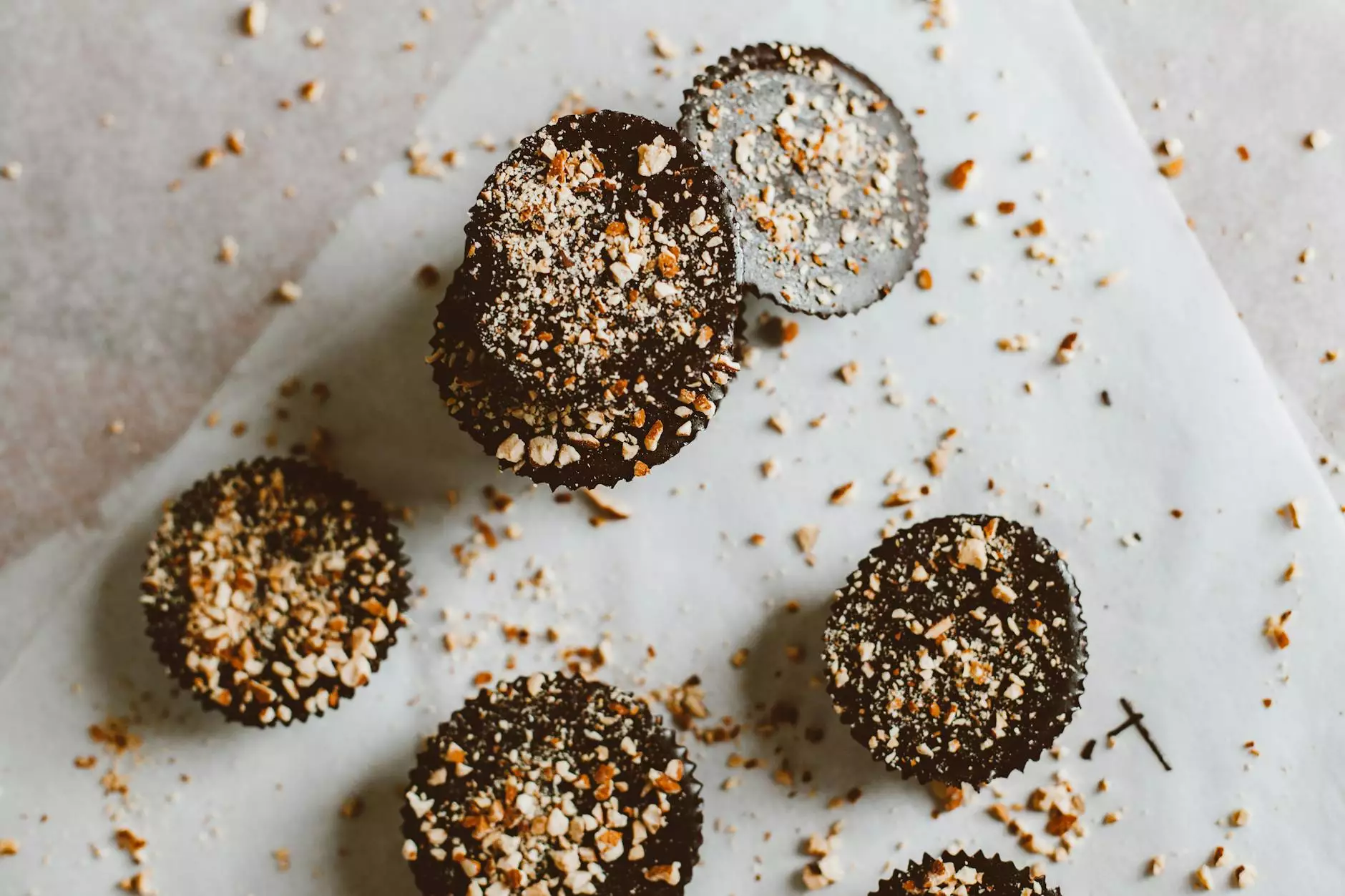
The die casting mould factory industry is a vital segment within the broader manufacturing landscape, offering unparalleled precision and efficiency in the production of metal components. As we delve into this subject, we will unpack the intricacies of the die casting process, the advantages it presents for businesses, and a deep look at how manufacturers, like DeepMould.net, are paving the way in this competitive market.
Understanding Die Casting
Die casting is a manufacturing process that involves forcing molten metal under high pressure into a die or mold. This technique is renowned for its ability to produce complex shapes with outstanding detail. The most commonly used metals in this process include aluminum, zinc, and magnesium. The die casting process not only ensures high precision in dimensions but also significantly reduces the need for secondary machining.
Key Benefits of Die Casting
The advantages of utilizing a die casting mould factory are numerous, making it a go-to solution for various industries. Here are a few key benefits:
- High Accuracy and Consistency: Die casting provides impressive dimensional accuracy, ensuring each piece meets stringent specifications.
- Enhanced Mechanical Properties: Cast parts have high structural integrity and excellent mechanical properties, making them suitable for demanding applications.
- Casting Complex Geometries: The process allows manufacturers to create intricate designs that would be difficult to achieve with other methods.
- Cost-Effectiveness: In high-volume production runs, die casting becomes highly economical due to the reduction in scrap rates and the speed of the manufacturing process.
- Surface Finish: Components can be manufactured with a superior surface finish, often eliminating the need for additional treatments.
The Die Casting Process Explained
1. Die Preparation
The first step in the die casting process involves preparing the dies. These molds are typically made from high-quality steel and must be carefully engineered to withstand the temperature and pressure of molten metal. The die design is crucial, affecting everything from the quality of the cast to the efficiency of production.
2. Melting the Metal
In this stage, the chosen metal (aluminum, zinc, or magnesium) is melted in a furnace. Precise temperature control is essential to ensure that the metal is at the right viscosity for casting.
3. Injection of Molten Metal
Once the metal is molten, it is injected into the prepared die at high pressure. This rapid injection fills the mold completely, allowing for the intricate details of the die to be captured in the final product.
4. Cooling and Solidification
After the die is filled, the molten metal begins to cool and solidify, taking on the shape of the mold. Cooling times vary depending on the metal used and the complexity of the design.
5. Ejection and Finishing
Once cooled, the die is opened, and the finished part is ejected. The components may then undergo finishing processes such as machining, plating, or surface treatment, depending on the requirements.
Applications of Die Casting
Due to its versatility, die casting finds applications across multiple sectors:
- Automotive Industry: Many parts, such as engine blocks, transmission cases, and brackets, are produced using die casting.
- Consumer Electronics: Die casting is employed in the production of housings and structural components for various electronic devices.
- Aerospace Components: Critical aerospace parts are manufactured with high degrees of precision and quality assurance.
- Medical Devices: The medical industry benefits from die casting in the production of precision instruments and devices.
- Telecommunications: Metal housings and parts for electronic devices are commonly produced through die casting.
Why Choose DeepMould.net for Your Die Casting Needs?
Choosing the right manufacturer is crucial for the success of any project involving die casting. At DeepMould.net, we pride ourselves on our state-of-the-art facilities and our commitment to quality. Here are some reasons why we stand out:
1. Advanced Technology and Expertise
Our factory is equipped with the latest die casting technology, allowing us to maintain high precision in every component we produce. Our staff consists of seasoned professionals who understand the nuances of the die casting process and work diligently to exceed customer expectations.
2. Custom Solutions
At DeepMould.net, we recognize that each client has unique needs. We offer tailored solutions, working closely with customers to develop die casting products that fit their specific requirements.
3. Quality Assurance
Quality is at the forefront of our production process. Every product undergoes rigorous quality control measures, ensuring that every die casting component meets industry standards and client specifications.
4. Competitive Pricing
We understand the importance of cost in manufacturing. Our efficient processes and economies of scale enable us to offer competitive pricing without sacrificing quality.
Conclusion: The Future of Die Casting
The die casting mould factory sector is poised for continued growth as industries seek faster, more efficient production methods with higher precision. As businesses like DeepMould.net continue to innovate and adapt to market demands, the array of applications and capabilities of die casting will expand, offering unprecedented opportunities for manufacturers and consumers alike.
For those looking to leverage the power of die casting, partnering with a reliable and experienced die casting mould factory is imperative. With our extensive expertise, commitment to quality, and customer-centric approach, DeepMould.net is ready to meet your die casting needs and deliver outstanding results. Consider us your partner in navigating the exciting possibilities of die casting.