Understanding Lathe Machine Parts: Key Elements in Metal Fabrication
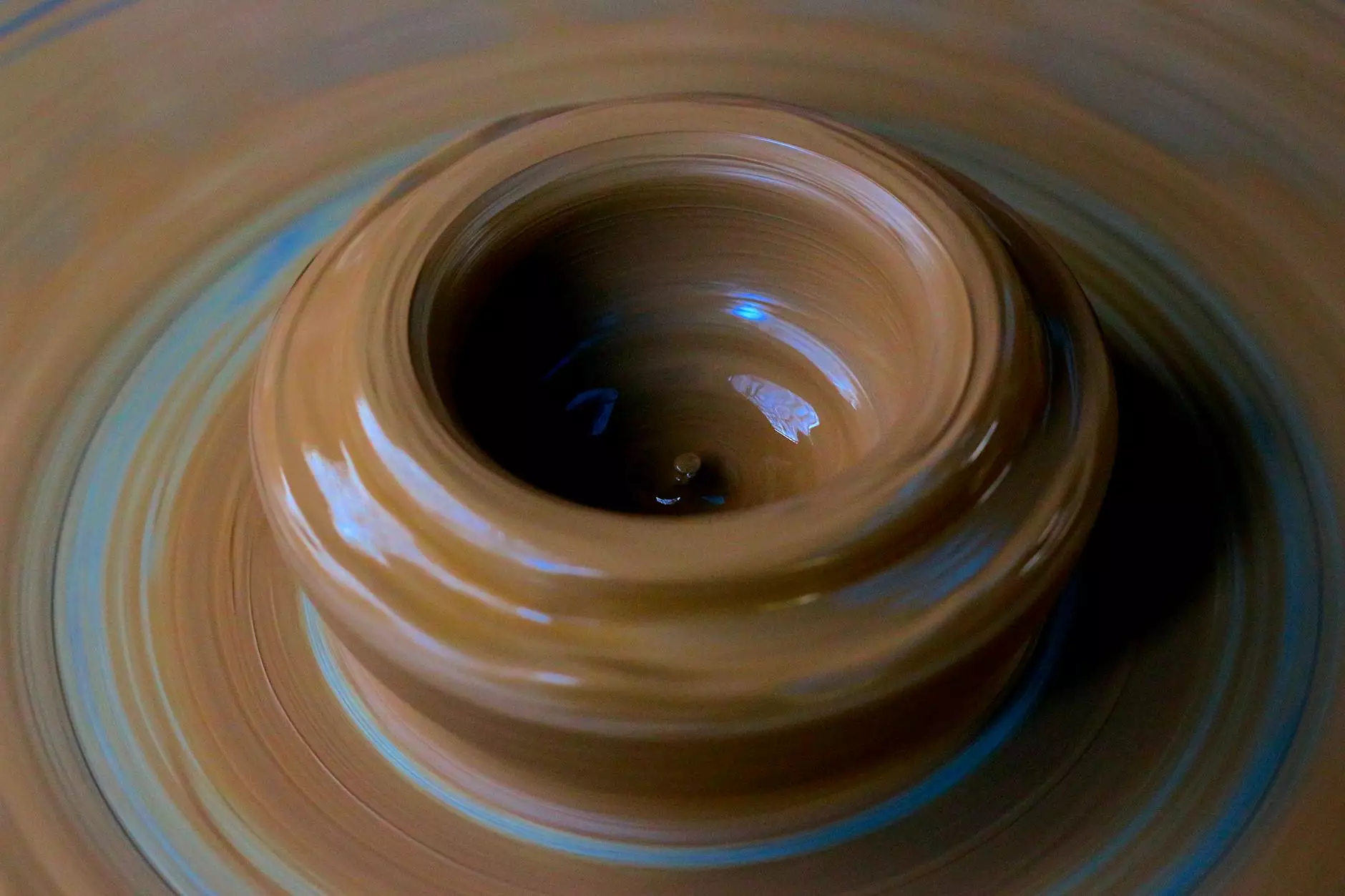
The world of metal fabrication is both intricate and fascinating, involving a vast array of processes, tools, and machinery. Among the most crucial instruments in this field are lathe machines, known for their ability to shape materials with exemplary precision. This article dives deep into the lathe machine part and highlights their significance within the broader context of metal fabrication.
What is a Lathe Machine?
A lathe machine is an essential tool used in the fabrication and manufacturing sector, particularly for shaping metal and other materials. It functions by rotating the workpiece around a fixed axis while a cutting tool is applied to its surface, allowing for various processes including turning, drilling, and threading. The vital components that make up a lathe machine, which are collectively referred to as lathe machine parts, play significant roles in ensuring efficiency, accuracy, and quality in machining operations.
The Essential Components of a Lathe Machine
Every lathe machine comprises several key parts, each contributing uniquely to its operation. Below, we explore these lathe machine parts and their specific functions:
- Bed: The foundation of the lathe, the bed provides support and stability. It is made from solid cast iron and spans the length of the machine.
- Headstock: Located at one end of the bed, the headstock houses the motor, pulleys, and the spindle, which holds and rotates the workpiece.
- Tailstock: Positioned opposite the headstock, the tailstock provides additional support for longer workpieces and houses the tool post for drilling operations.
- Carriage: This component moves along the bed and holds the cutting tools, allowing operators to precisely control the tool's position.
- Cross Slide: Part of the carriage, the cross slide moves horizontally to facilitate lateral adjustments of the cutting tools.
- Tool Post: Mounted on the carriage, the tool post secures the cutting tools in place and allows for easy adjustment.
- Spindle: The spindle is a rotating shaft within the headstock, transmitting power from the motor to the workpiece.
- Chuck: The chuck is a clamping device that grips the workpiece securely. Different types of chucks are available, including three-jaw and four-jaw chucks.
- Feed Mechanism: This system controls the movement of the carriage and the advancement of the cutting tool.
- Power Transmission: This includes belts, gears, and other components that transfer power from the motor to the spindle, enabling the lathe to operate effectively.
The Importance of Each Lathe Machine Part
Each of the lathe machine parts plays a pivotal role in ensuring the machine operates smoothly and effectively. Understanding their functions can help in troubleshooting, maintenance, and performance optimization. Here’s a detailed examination of why each component is crucial:
1. Bed
The bed is the backbone of a lathe machine. Its rigidity and stability are fundamental because any flex or deformation can lead to inaccuracies in the machining process. A well-designed bed can compensate for vibrations and provide a level base, ensuring that the workpiece remains aligned throughout the machining process.
2. Headstock
The headstock is where the power originates. It houses the motor and is responsible for the rotation of the spindle, which holds the workpiece. The speed at which the spindle rotates can often be adjusted, allowing the operator to select the right speed for different materials and cutting processes. A high-quality headstock contributes significantly to the overall performance and longevity of the lathe.
3. Tailstock
The tailstock supports longer workpieces, preventing them from bending or flexing during the machining process. It can also be adjusted to accommodate different lengths of material, making it a versatile component. Inclusion of a drill bit or other tools in the tailstock can enhance the machine's capabilities, allowing for operations like end drilling.
4. Carriage
The carriage is essential for the precise control of tooling movements. It allows the cutting tool to move longitudinally and laterally, enabling various operations such as turning and grooving. An efficient carriage design can minimize friction, enhancing the ease of use and precision during machining.
5. Cross Slide
The cross slide is integral for lateral movement adjustments. This component allows for fine-tuning the cutting depth and feed rate. Precision in this part allows for complex part designs and finer finishes.
6. Tool Post
The tool post is critical for securing the cutting tool at the correct angle and depth. The ability to easily change and adjust the tools is vital for efficiency, particularly in production environments requiring multiple operations on the same workpiece.
7. Spindle
The spindle is where the real action happens. As the element that directly rotates the workpiece, its design and quality can impact everything from vibration levels to heat generation. Ensuring that the spindle is well-maintained will yield better performance and higher quality output.
8. Chuck
The chuck must grip the workpiece securely, providing a stable platform for machining operations. The choice between a three-jaw and four-jaw chuck can depend on the type of workbeing conducted—three-jaw chucks are often quicker to set up, while four-jaw chucks allow for more precise centering.
9. Feed Mechanism
This component determines how smoothly and effectively the carriage moves. A finely tuned feed mechanism allows for consistent machining operations, contributing to overall productivity and quality of the finished product.
10. Power Transmission
The effectiveness of the power transmission system within a lathe machine can influence its operation significantly. Ensuring that all belts, gears, and pulleys are in optimum condition is essential for achieving desired results in machining tasks.
Advantages of Understanding Lathe Machine Parts
For anyone involved in metal fabrication, possessing a deep understanding of lathe machine parts can lead to numerous advantages:
- Improved Maintenance: Recognizing how each component functions can aid in early detection of potential issues, allowing for more timely repairs.
- Enhanced Precision: Knowledge of adjustments and settings can significantly improve the accuracy of machining tasks, resulting in better quality components.
- Efficiency Gains: Understanding how to optimize the use of each lathe part can enhance operational efficiency, leading to quicker turnaround times and lower costs.
- Effective Troubleshooting: With a comprehensive understanding of each part, operators can easily troubleshoot problems when they arise, minimizing downtime.
- Skill Development: A thorough knowledge of lathe components contributes to overall skill development in machining, encouraging deeper learning and expertise.
Best Practices for Using Lathe Machine Parts
To maximize the performance and lifespan of lathe machine parts, adhering to best practices is essential:
Regular Inspections
Conduct frequent inspections of all lathe machine parts. Check for wear, damage, and misalignment. Addressing minor issues before they escalate can save time and money in the long run.
Proper Maintenance
Routine maintenance, including cleaning and lubrication, is crucial for smooth operation. Ensure that moving parts are well-lubricated to reduce friction and wear.
Use Quality Materials
When replacing parts, invest in high-quality materials that match OEM specifications. This can significantly improve machine performance and reliability.
Operator Training
Ensuring that operators are well-trained in using the lathe machine and understanding its parts can greatly enhance productivity and safety.
Documentation and Record Keeping
Keep detailed records of all maintenance work and repairs. This documentation can help in identifying patterns that may signal larger underlying issues.
The Future of Lathe Machines in Metal Fabrication
The evolution of lathe machines and their parts is continuously progressing, driven by advancements in technology and manufacturing processes. The integration of CNC (Computer Numerical Control) systems has revolutionized the industry, allowing for unparalleled precision and automation. While traditional lathe machines will always have a place in fabrication, the future undoubtedly leans towards smarter, more efficient solutions.
As the industry evolves, the demand for skilled machinists who understand both traditional and modern lathe machine parts will continue to grow. Companies like DeepMould.net are at the forefront of this evolution, providing essential components and knowledgeable support to help businesses thrive.
Conclusion
In summary, the intricate workings of lathe machines and their parts play a vital role in the realm of metal fabrication. A comprehensive understanding of each lathe machine part allows operators and technicians to enhance their machining processes, leading to increased efficiency, accuracy, and quality outputs. By adhering to best practices and staying informed about advancements in technology, businesses can ensure they remain competitive in an ever-changing landscape.
For businesses looking to optimize their metal fabrication processes and improve their lathe machine operations, DeepMould.net offers a wealth of knowledge, quality components, and excellent service that can help achieve those goals.